Atomizing facilities
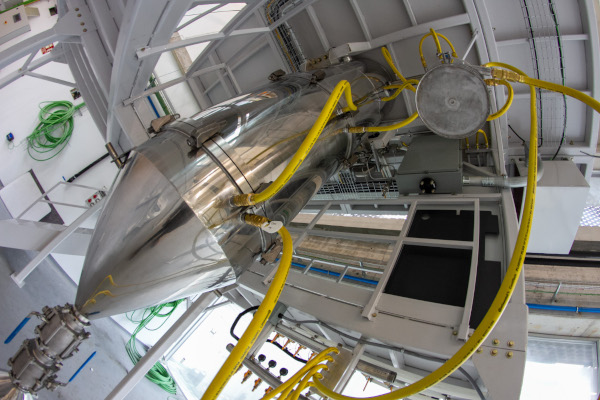
By Arcast. Its capacity ranges from 30 to 250 kg.
This unit has the capacity to melt in vacuum (10E-2 mbar) or controlled (low oxygen) atmospheres. It uses argon and nitrogen gases in the atomization process and has a system that can heat the atomizing gas up to 500 ºC.
It is The HERMIGA 75/3 from PSI, with a 3 kg capacity.
This is a dual atomization unit that is capable of high pressure water (up to 1000 bar) or gas atomization and of melting in vacuum (10E-2 mbar) or controlled (low oxygen) atmospheres.
The unit’s maximum operating temperature is 1750º C (using refractory crucibles) and it can atomize using argon, nitrogen or helium. This atomization unit is suitable for producing small quantities for researching and developing new materials and for developing new atomization systems.
-
Ceit has the full range of equipment necessary to achieve the most complete chemical analysis, PSG (particle size distribution), and bulk and mechanical properties
-
SPECTRO SPECTROMAXx mass spectrometer
-
ICP analyzer from Variant for running checks on the final compositions of the products produced
-
Two devices by LECO, the CS-200 and TC 400, for measuring oxygen, sulfur, carbon and nitrogen
-
MASTERSIZER 3000 laser diffractometer by Malvern
-
Ceit uses scanning and optical microscopy techniques to characterize morphology: a FEG-SEM from ZEISS and JEOL and an internally constructed FIB instrument
-
Ceit has the equipment to perform advanced mechanical property tests